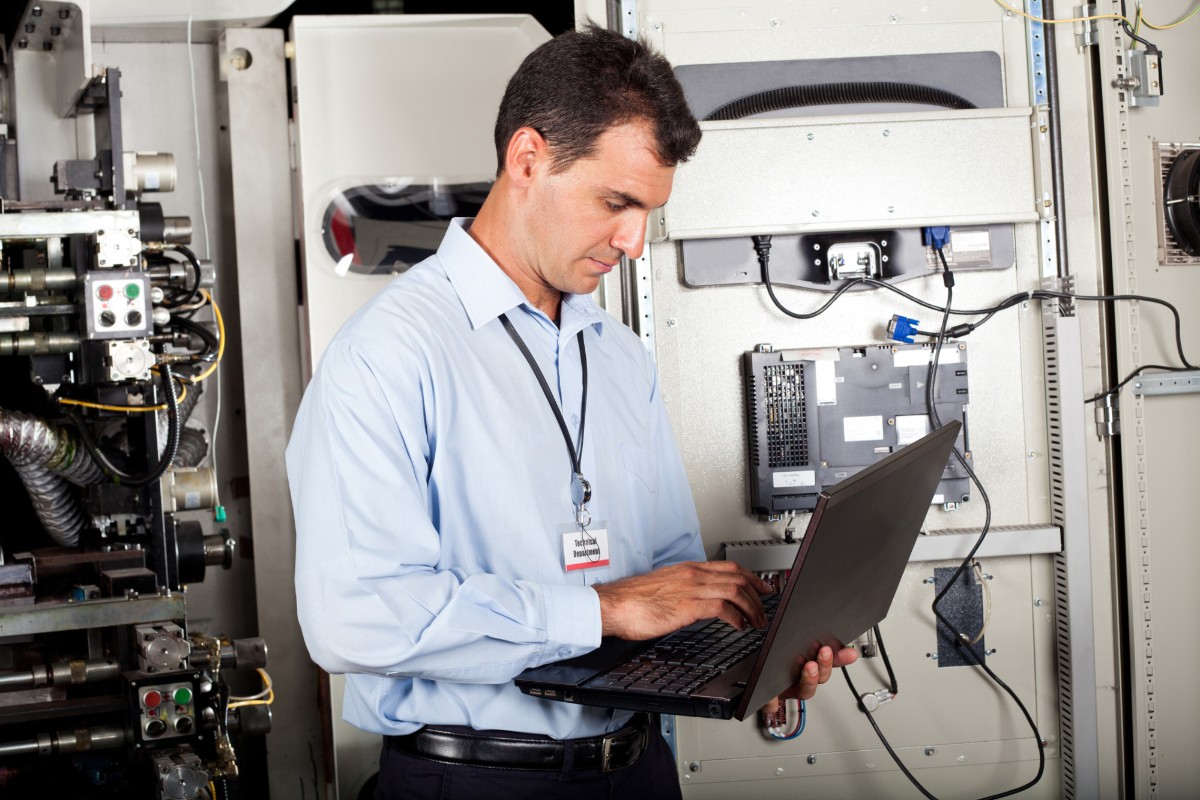
7 práticas para fazer uma gestão de manutenção eficiente na empresa
A manutenção industrial de máquinas e equipamentos deve ser regular para que o parque fabril esteja sempre operando com bons níveis de segurança e produtividade, concorda? No entanto, sem um planejamento das ações, você pode ter uma dificuldade maior em controlar riscos e, com isso, ter custos elevados e um tempo de inatividade maior.
Por isso, a gestão de manutenção é protagonista no sucesso da indústria. Com iniciativas guiadas por dados, objetivos bem estabelecidos, tarefas definidas e procedimentos claros, a rotina da manutenção da indústria passa por uma grande otimização que impacta diretamente os resultados.
Neste post, separamos 7 passos fundamentais para ter um gerenciamento de manutenção eficiente. Anote aí!
1. Mapeie os fluxos de manutenção atuais
O primeiro passo de qualquer mudança na estratégia é entender com o que você está trabalhando. Para fazer a transição com sucesso para uma gestão de manutenção mais eficiente, você deve coletar dados sobre o estado atual das coisas. Avalie variáveis como:
- tempo médio entre falhas de máquinas — MTBF;
- tempo médio de paradas não planejadas;
- custos médios com trocas de peças danificadas;
- índice de refugo na produção decorrente de falhas operacionais etc.
2. Entenda a diferença entre os tipos de manutenção
Com base no mapeamento realizado, identifique quais são os recursos gastos pela sua empresa em cada um dos tipos de manutenção, considerando matéria-prima, custos financeiros, espaço físico, deslocamento de operadores etc.
Uma boa gestão de manutenção deve sempre priorizar os fluxos de cuidados preventivos e preditivos. Então, analise seus resultados e estabeleça objetivos que proporcionem a redução do uso de recursos com correções.
Manutenção corretiva
Tende a ser de natureza não planejada e esporádica, com o objetivo de identificar, isolar e corrigir uma falha, por exemplo, a troca de alguma peça com superaquecimento. As ações corretivas farão com que o equipamento volte a funcionar, mas isso não significa que funcionará da melhor maneira possível.
Manutenção preventiva
A manutenção preventiva envolve verificações periódicas com a intenção de evitar falhas antes que elas aconteçam. Ela melhora a detecção de falhas e reduz as ações de manutenção corretiva.
Manutenção preditiva
Um plano de gerenciamento de manutenção preditiva é feito monitorando as condições do equipamento com técnicas como:
- análise do alinhamento e nivelamento de peças e componentes do maquinário, que pode indicar desvios comprometedores de qualidade na indústria e eficiência produtiva;
- análise de vibração de peças, que podem indicar falha iminente ou desalinhamento;
- análise acústica, que ajuda a detectar vazamentos de líquidos ou gases;
- análise da lubrificação de máquinas, que é essencial para a conservação do equipamento e para a segurança da operação;
- termografia por infravermelho, para detectar temperaturas excessivamente altas.
3. Invista no gerenciamento computadorizado
No ambiente de fabricação moderno, as soluções industriais voltadas para a digitalização não são mais apenas uma opção. A manutenção preventiva, corretiva e reativa pode ser gerenciada usando planilhas e métodos manuais.
A implementação de manutenção preditiva econômica e eficiente, no entanto, requer mais poder computacional. Felizmente, os sistemas de gestão de manutenção computadorizados (CMMS, sigla para Computerized Maintenance Management Software) estão mais acessíveis e fáceis de usar do que nunca.
A mudança para tecnologias baseadas na nuvem significa que não são mais necessários grandes investimentos de capital em sistemas locais, além de representar a otimização de processos e a melhoria na qualidade da gestão.
4. Adote um cronograma de manutenção
Com dados e softwares em mãos, você pode começar a mudar de reativo para proativo. Seu software CMMS e as últimas datas de manutenção fornecerão seu cronograma inicial de manutenção preventiva e preditiva.
O planejamento do cronograma é essencial para evitar a reserva dupla de um técnico, maximizando a eficácia. Lembre-se de que um plano de gerenciamento de manutenção corretiva não será eliminado, mas deve ser progressivamente menor.
5. Integre os setores responsáveis
Uma gestão de manutenção perfeitamente planejada é inútil se você não tiver as peças ou os técnicos necessários para executá-lo. Por isso, pense em estratégias para sincronizar ordens de serviço, colaboradores, peças de reposição e programas de manutenção.
Por exemplo, a manutenção normalmente requer o consumo de materiais. Por isso, é importante ter uma boa comunicação e planejamento de compras para o estoque de reposição.
Outro ponto é o papel dos colaboradores e gestores responsáveis pela rotina preventiva. É importante que cada um saiba exatamente os impactos das suas tarefas de manutenção agendadas para o funcionamento do chão de fábrica como um todo.
Uma dica é terceirizar alguns serviços regulares de manutenção, especialmente em tarefas altamente especializadas ou que demandam o uso de equipamentos diferenciados.
6. Acompanhe métricas e indicadores de performance
É possível promover melhorias à medida que mais operadores e gerentes estão atentos aos KPIs (sigla em inglês para Indicadores-Chave de Performance). No entanto, o rastreamento é apenas a primeira parte da equação de otimização — dados sólidos são a base para melhorias efetivas.
É interessante acompanhar indicadores como:
- tempo médio de operação antes da falha;
- tempo médio para reparo;
- porcentagem de manutenção planejada e não-planejada.
Para ter análises confiáveis, o ideal é passar algumas semanas acompanhando o estado atual das coisas antes de implementar mudanças na estratégia. Isso funcionará como uma linha de base que pode ser medida em relação ao desempenho futuro e para criar uma gestão de manutenção mais centrada em objetivos.
7. Faça ajustes orientados em dados
Com uma imagem clara da sua linha de base de desempenho, o efeito de novas alterações pode ser medido em dias, semanas e meses. Tente introduzir apenas uma ou duas novas alterações por vez para limitar o número de variáveis que afetam suas métricas.
Isso também ajuda a isolar as alterações que acabam tendo efeitos negativos. Uma coisa a ter em mente é que não é necessário realizar uma revisão completa de uma só vez. As restrições de orçamento podem fazer com que você execute manutenção preventiva inicialmente antes de introduzir técnicas de manutenção preditiva mais eficazes.
O rastreamento da efetividade de manutenção preditiva de um ou dois ativos importantes pode ajudá-lo a determinar se e quando deve ser implementado em mais máquinas industriais. A análise de manutenção centrada na confiabilidade oferece uma estrutura para melhorar a estratégia em toda a empresa.
Enfim, a gestão de manutenção é essencial para ter mais controle sobre o risco de falhas. Sem ela, a empresa fica sujeita ao desperdício de produção e de ativos, aos custos elevados com manutenção corretiva, à perda de qualidade e de produtividade. Tudo isso representa impactos negativos na posição competitiva.
Para potencializar a sua gestão de manutenção, a ajuda de uma empresa especializada é decisiva. Por isso, entre em contato com a gente e conheça nossos serviços!
Deixe um comentário
7 comentários.